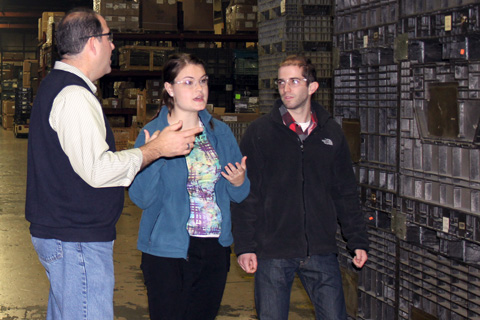 |
Oakland University students Britney Helsing and Chris Miklasz meet with Tom Grant, chief information officer at Airboss Flexible Products in Auburn Hills, to discuss ways to streamline operations. |
“Go to the Gemba” is the tagline in Special Instructor Mark Doman’s HRD 344/POM 480 class, where students are using Lean principles to help local businesses and nonprofits achieve cost-savings and improve efficiency.
The course is designed to teach students how successful “Lean kaizen,” or process improvement events, are conducted in different areas of industry. The class focuses on six main areas: Lean philosophy, Lean tools and techniques, team building, kaizen methodology, organization change, and presentation and facilitation.
To support hands-on learning, the class is divided into six student teams, each partnered with a different company or nonprofit organization. Nick Taylor is a team leader for students working on a project with Southfield-based Orchid Orthopedic Solutions.
“This class is different from most of the other business classes because Professor Doman allows us to not only learn in class, but also to apply the material immediately after we learn it,” said Taylor, a senior majoring in operations management. “We go to the Gemba, or in other words, go to the place where the work is being done, outside of class. We are investigating the actual problems – identifying and analyzing the wasteful activity – within the company.”
Doman launched the course in 2013 with support from a Pawley Institute Fellowship. He brings extensive experience to Oakland, having worked on Lean-oriented initiatives for companies such as Ford Motor Company and AT&T. In his classes, Doman emphasizes the relevance of Lean principles in today’s workplace.
“OU is at the forefront of Lean education. We are fortunate to have one of the Lean pioneers, Dennis Pawley, so involved with our courses,” Doman said. “Our students are learning a different way of thinking and problem-solving, while at the same time, gaining valuable experience working on real-world problems with our sponsor organizations. At the end of the course, our students can show future employers that they can take the lead in solving their problems.”
The other participating organizations are Fitzpatrick Manufacturing Company, General Motors, Airboss Flexible Products, Eaton Steel Bar Company and the Detroit Historical Society. Each student team meets with company leaders to discuss ways to streamline operations.
“Lean is a very valuable skill set that can be applied to many different areas in manufacturing and service-oriented businesses,” said Brad Carson, who leads the team partnering with the Detroit Historical Society (DHS). “This class is an excellent example of how academic training translates to real-world business solutions.”
Carson and his team have visited the Detroit Historical Museum and the Detroit Great Lakes Museum with the goal of improving inventory management at the two sites. At the end of the course, the team will present its recommendations to DHS leaders.
“We’re looking at their processes and trying to get down to the root cause of the problem,” Carson explained. “Once we identify the cause, we’ll be able to present countermeasures to remedy the problem. We’re working with the DHS leaders to establish a solid foundation, a standard process that everyone can follow that will improve quality, reduce cost and ensure timely delivery of goods.”
Andrew Mandley, an
Honors College member, heads the General Motors team, which is working at the company’s Pontiac Redistribution Center. He said that GM employees have been involved every step of the way as the team has worked on a process for the storage and destruction of material identification tags.
“We have already identified multiple opportunities for improvement within the process, but we will continue to explore more throughout the semester as we prepare our final presentation for all of the process stakeholders,” Mandley said. “The Lean approach provides an opportunity to improve almost any process, so I'm looking forward to applying it in my own work throughout the rest of my life.”
HRD 344 is the preferred elective for Industrial and Systems Engineering students and will satisfy the University’s general education requirement for knowledge application integration.
For information about the Pawley Lean Institute, visit the website at oakland.edu/lean.